Precision Components Manufacturers: A Driving Force in Modern Manufacturing
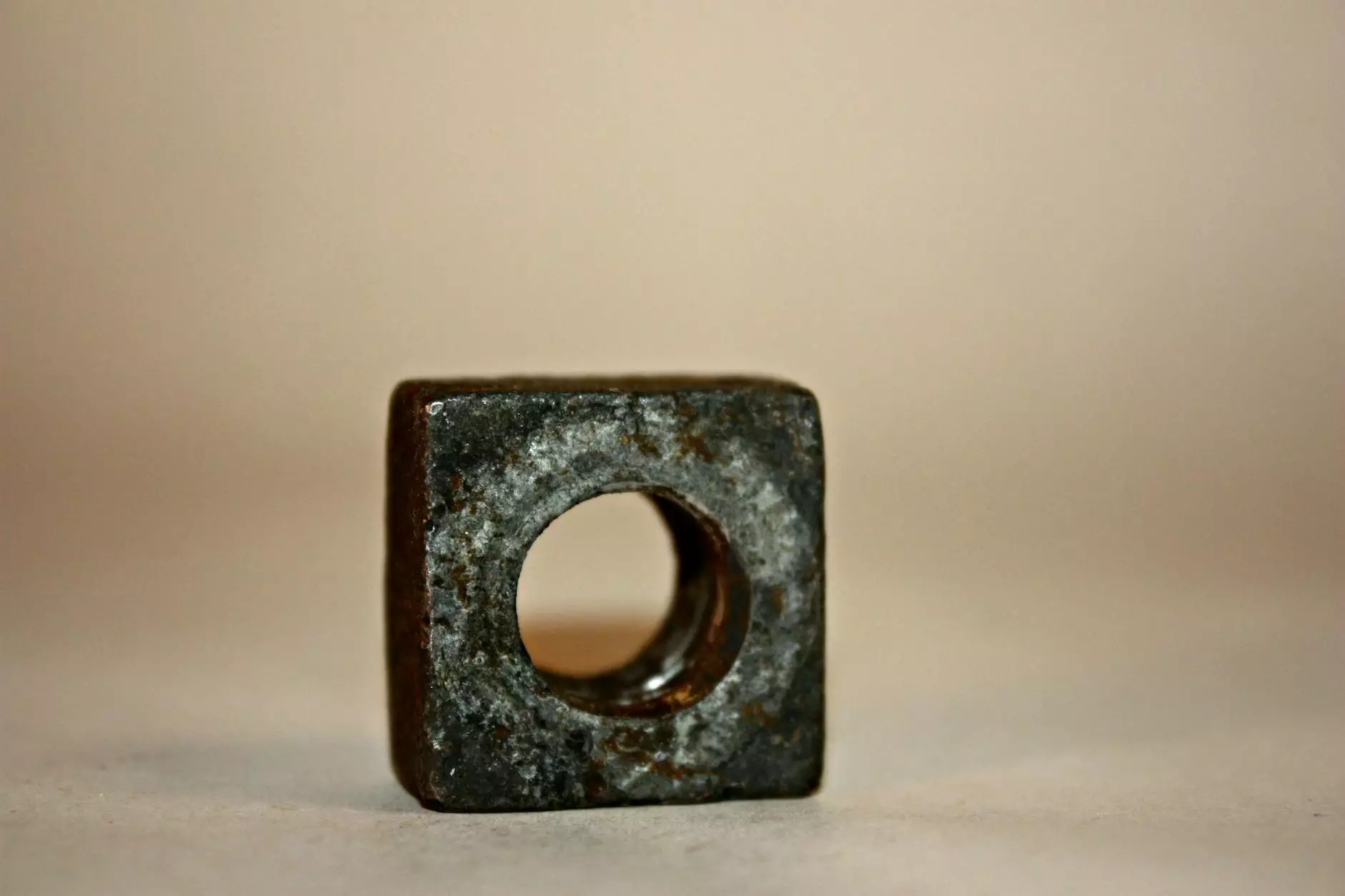
In today's rapidly evolving industrial landscape, precision components manufacturers play an essential role in ensuring the efficiency, reliability, and quality of various products across multiple sectors. From automotive and aerospace to electronics and healthcare, the demand for high-quality, precision-engineered components has never been greater. This article delves into the significance, processes, benefits, and innovations within the realm of precision component manufacturing.
The Importance of Precision in Manufacturing
Precision manufacturing refers to the process of creating parts and components with extreme accuracy and minimal tolerances. The significance of precision in manufacturing cannot be overstated, as even the tiniest deviation in size or shape can lead to substantial issues in performance and functionality. Here are some reasons why precision is critical:
- Quality Assurance: Ensuring that components meet strict tolerances helps in maintaining overall product quality.
- Enhanced Performance: Precision components operate more efficiently, contributing to better end-product performance.
- Cost Efficiency: High precision reduces waste and rework, leading to cost savings in production.
- Safety: In sectors like aerospace and medical devices, precision is paramount to ensure safety and reliability.
Key Processes in Precision Component Manufacturing
Precision components manufacturers employ a variety of advanced fabrication techniques to deliver high-quality products. Here are some of the most common processes:
CNC Machining
CNC (Computer Numerical Control) machining has revolutionized the manufacturing industry by offering unmatched precision and repeatability. With CNC machines, manufacturers can produce intricate parts from a wide range of materials—such as metals, plastics, and composites—by controlling cutting tools with computer programming. Benefits of CNC machining include:
- High repeatability and consistency in production.
- Capability to create complex geometries that would be impossible to achieve manually.
- Reduced human error through automated processes.
Injection Molding
Injection molding is a highly efficient process used predominantly for producing plastic components. In this technique, melted plastic is injected into a mold cavity to create predefined shapes. This process is not only cost-effective for high-volume production but also provides:
- High precision in part dimensions.
- The ability to produce complex designs with minimal secondary processing.
- Rapid cycle times for increased production rates.
Sheet Metal Fabrication
Sheet metal fabrication involves cutting, bending, and assembling metal sheets to produce a wide array of components. Manufacturers utilize techniques such as laser cutting, punching, and welding to maintain precision. Key advantages include:
- Durability and strength of metal components.
- Versatility in design and application.
- Cost-effective solutions for both low and high-volume production.
Industries Benefiting from Precision Components
The versatility of precision components makes them indispensable across various industries. Some key sectors include:
Aerospace
The aerospace industry demands the highest standards of safety and reliability. Precision components are critical in various applications, such as:
- Aircraft engines.
- Navigation systems.
- Structural elements.
Automotive
In the automotive industry, precision components enhance vehicle safety, performance, and fuel efficiency. Applications include:
- Engine components.
- Transmission systems.
- Instrumentation and control systems.
Electronics
The electronics sector requires ultra-precision components for device miniaturization and performance. This includes:
- Chip carriers and substrates.
- Connectors and interfaces.
- Printed circuit boards (PCBs).
Medical Devices
Precision components are fundamental in the manufacturing of medical devices, where reliability can directly affect patient health. Applications include:
- Surgical instruments.
- Implantable devices.
- Diagnostic equipment.
The Role of Technology in Precision Manufacturing
Advancements in technology have significantly impacted precision manufacturing. Here are some technological innovations that are shaping the industry:
3D Printing
3D printing or additive manufacturing has entered the precision components manufacturing space, offering the ability to create complex geometries directly from digital models. Key advantages include:
- Reduction in material waste compared to traditional subtractive methods.
- Speedy prototyping, enabling rapid iterations in design.
- Ability to produce customized components efficiently.
Automation and Robotics
Automation in manufacturing processes minimizes human intervention, enhancing both speed and precision. Robotics perform repetitive tasks with high accuracy, thus:
- Improving productivity.
- Reducing the risk of human error.
- Enabling 24/7 operation in facilities.
IoT Integration
The Internet of Things (IoT) has started to influence precision manufacturing by allowing real-time data collection and monitoring. This integration offers:
- Enhanced decision-making through analytics.
- Predictive maintenance to avoid downtimes.
- Improved supply chain management.
Challenges in Precision Component Manufacturing
While there are numerous advantages in precision components manufacturing, there are also challenges that manufacturers face:
Supply Chain Disruptions
Global events can lead to significant supply chain disruptions, affecting the availability of raw materials and components necessary for production.
Cost Management
Maintaining high-quality output while managing costs is a crucial balancing act for precision manufacturers, given the increasing competition and market pressures.
Technological Adaptation
The need to stay current with rapidly evolving technologies requires significant investment in training and equipment, which can be a barrier for some manufacturers.
Future Trends in Precision Manufacturing
The landscape of precision components manufacturing is continuously evolving. Here are some emerging trends:
Sustainability Practices
With increasing awareness of environmental responsibility, manufacturers are implementing eco-friendly practices. This includes:
- Recycling materials.
- Energy-efficient manufacturing processes.
- Minimizing waste generation.
Continued Automation
The trend toward greater automation is expected to continue, driven by the need for efficiency and precision. This will likely involve further integration of AI and machine learning.
Advanced Materials
Research into advanced materials, including composites and smart materials, is paving the way for the next generation of precision components that are lighter, stronger, and more efficient.
Conclusion
In summary, precision components manufacturers are essential players in the modern manufacturing ecosystem. They drive quality, efficiency, and innovation across various industries, ensuring that products meet the demands of an ever-evolving market. As technology advances and new trends emerge, the future of precision manufacturing looks bright, promising continued growth and enhanced contributions to global industries.
For those looking to engage with a leader in the field of precision components manufacturing, Deep Mould offers a commitment to quality and excellence, serving as a significant resource for industries requiring the highest standards of precision.